.jpg?width=1000&height=665&name=BESPOKE%20PROFILES%20HUBBLE%20(2).jpg)
WHY CHOOSE US?
Custom profiles, purpose built to fit your project
Bespoke profiles require a custom tool to produce, but allow us to create a section of any design.
Trouble finding the right profile?
Most projects that use a bespoke section begin with an unsuccessful search for a standard profile.
If you've tried to find the perfect standard for your project, but it doesn't seem to exist, there's no need to worry.
Our experience allows us to help you develop a custom profile, within a short period of time, that exactly serves your requirements.
Already have a design in mind?
If you've already developed the perfect profile for your project, simply supply us with a copy of the drawings.
To help ensure your offer design is workable, we offer design advice (and assistance if required) and prototypes too!
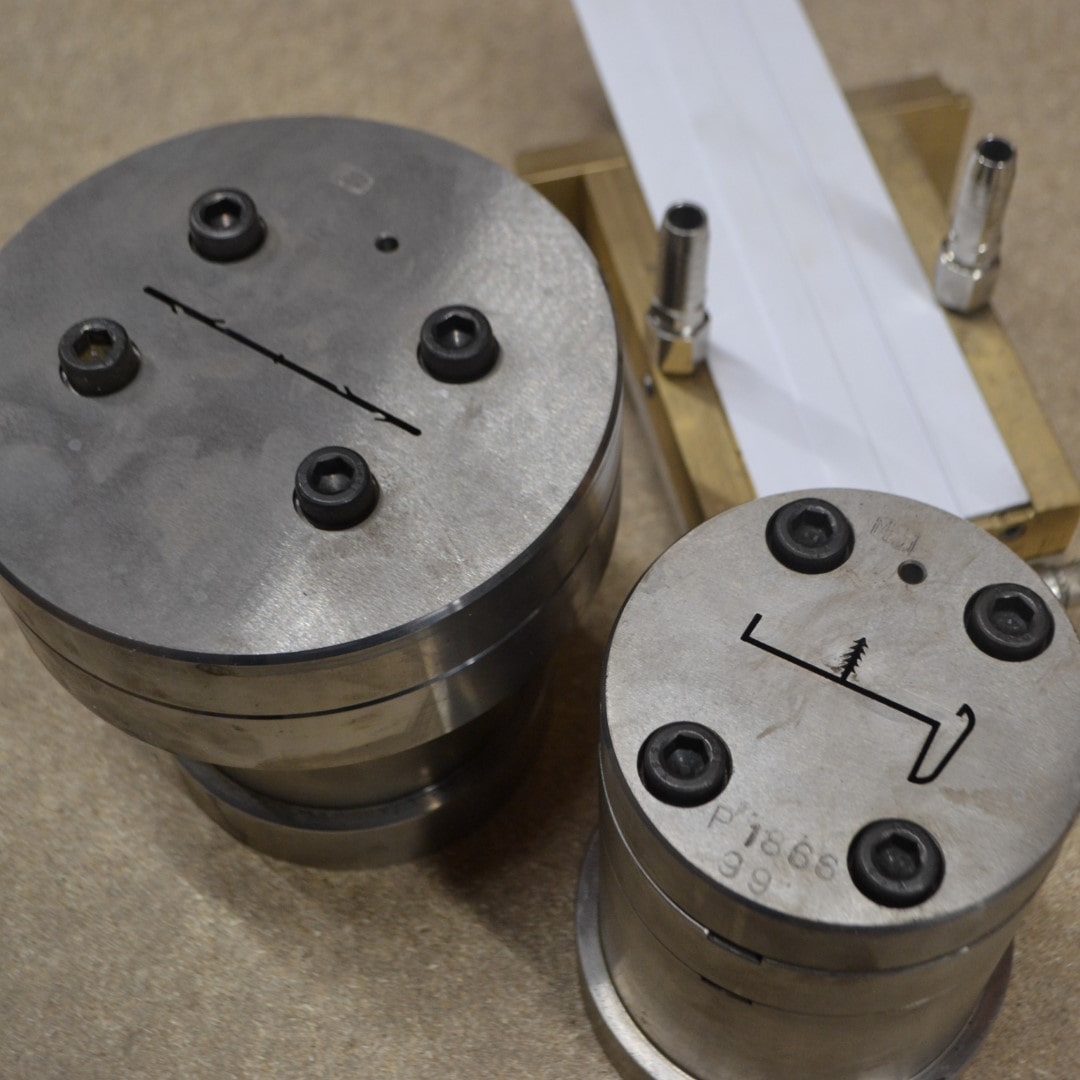
Tool Making
Enhancing the efficiency and productivity of your extrusions starts with the right dies. To ensure the highest quality tools for your profiles, we have established relationships with reliable and experienced tool makers so we can provide dies that meet the exact specifications of your extrusion for smooth production, minimal waste and consistent output.
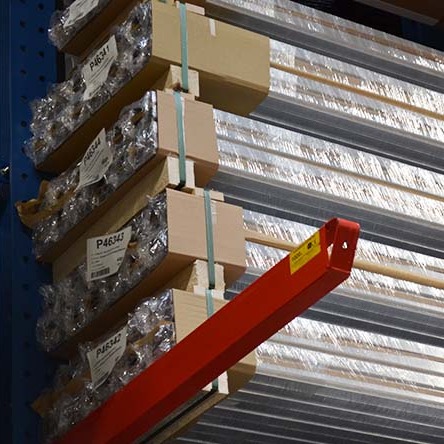
Stock Holding
A combination of MOQ's (minimum order quantities) and a lack of floorspace can make purchasing aluminium extrusion time consuming, expensive and a drain on resources. Our solution? A flexible stock holding and delivery service designed to streamline your supply chain: we'll stock your goods, and deliver them in any quantity and on demand.
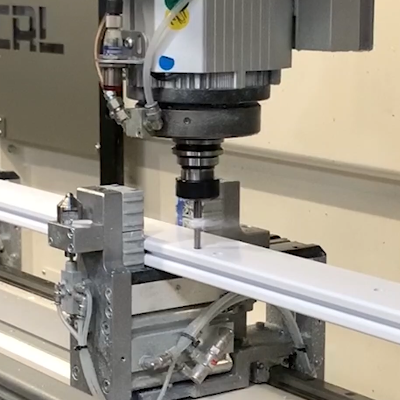
Fabrication
Our CNC machining centre and automated saw enable us to perform allow highly intricate and advanced fabrications with precision and efficiency. Meeting the demands of custom designs and high volume production includes adapting to evolving design requirements: offering flexible solutions for both standard and bespoke applications.
%20(Large)-min.jpg)
Your Design
We'll review your design and can help maximise its efficiency by helping with any design changes so you can get the most out of your component. Once your design is perfected, we can produce prototypes so you can make adjustments early on, saving time and costs later on and, we'll also supply you with the 2D and 3D drawings you can keep.