It’s surprising how many people believe their design will work and put it through the manufacturing process only to find certain parts of the design have failed. That’s why 3D printed prototype/samples are an excellent place for you to begin; it’s the most cost effective way of testing whether your design is going to work; giving you the chance to make alterations before having to pay the cost of a die and set up charges.
There are a lot of things to take into consideration when designing a die for extrusion, although each die design will be different, there are a set of general rules which govern the basics of die design.
Many extruders prefer to work with designs which are easier to produce, simple, similar wall thickness and symmetrical. It makes the production of the die more cost efficient for the extruder and gives the tool a longer life. Productivity also comes into play when extruders are evaluating new designs.
In this article, we are going to look into aluminium extrusion design and 5 common mistakes when designing a profile for extrusion.
1. Wall Thickness
A common challenge when designing a die for extrusion is getting the wall thickness right. For example, people will often design a profile which has thin walls or substantial variations in wall thickness which creates problems with metal flow during the extrusion process.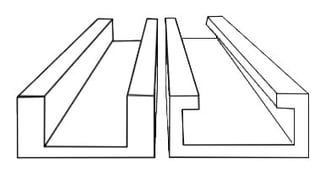
Other factors that influence wall thickness are the extrusion force and speed. Typically speaking, wall thickness depends on the general shape of the profile and whether it is solid or hollow. It is much harder to maintain flatness on a profile that has a thin wall and CCD (circumscribing circle diameter). Extrusion container size and ram pressure are also factors that can affect profile designs.
Having a wall thickness which is uniform throughout the profile also makes it easier to extrude.
2. Tolerances
There are many factors that affect tolerances, such as wall thickness, dimensions, size, profile type (solid or hollow) alloy used, overall profile shape, etc.
Productivity and price can also be affected when tolerances are tighter and should therefore be considered when designing your die.
Profiles which are designed with no understanding of dimensional limitations of the extrusion process should be rejected as they can cause many errors throughout the process.
Extrusion profile tolerances are generally controlled by BS EN 755-9 -which is a European standard specifying tolerances on dimensions and form for extruded aluminium and aluminium alloy profiles. Adhering to this standard ensures consistent quality and performance in various industrial applications and utilising it in your design means it can be extruded successfully.
Tolerances should always be considered in the design phase, if you are concerned about your tolerances or design, please contact one of our design experts.
3. Shapes & Corners
To assist in the flow of aluminium through the die, sharp corners should be avoided. Corners should ideally be radiused to assist extrusion flow. Blend radii should ideally be used to ease the flow from one mass area to the next, as this can help prevent witness lines along the surface of the profile.
4. Mating Components
There will be times when you will need to design an extrusion which features mating components.
Extrusions can be designed to slide, hinge or clip together, such as a clip fit for a two-part electronic enclosure. Simple designs are the most cost effective as they are easier to extrude so by having these mating components, it will reduce the assembly time significantly. You will need to think through the final assembly needs during your design phase to ensure that your design is extrudable and will fit with your mating components.
To understand more about designing for mating components and achieving the right extruded requirement for your aluminium profiles, please contact us.
5. Symmetry
The more unsymmetrical or unbalanced a shape, the less likely it is to remain straight or hold its shape accurately. It should be symmetrical where possible – There are often situations where this is impractical but with a little design assistance the profile can be made easier to extrude so you can achieve good tolerance and shapes.
In conclusion, avoiding these five common mistakes in aluminium extrusion profile design ensures optimal performance, cost-efficiency, and ease of manufacturing. By focusing on proper wall thickness, managing tolerances, avoiding sharp corners, managing tolerances, mating components and symmetry for assembly, you’ll achieve a superior and functional aluminium extrusion profile. Contact us today about your next aluminium extrusion project.